Hexapod
Six degrees of freedom motion platform for advanced research
The Hexapod is a compact six degrees of freedom parallel robotic motion platform capable of moving up to 100 kg at high acceleration. Unlike most commercially available Stewart platforms, the Hexapod is driven by superior electrical motors which make it precise, responsive and low-maintenance.
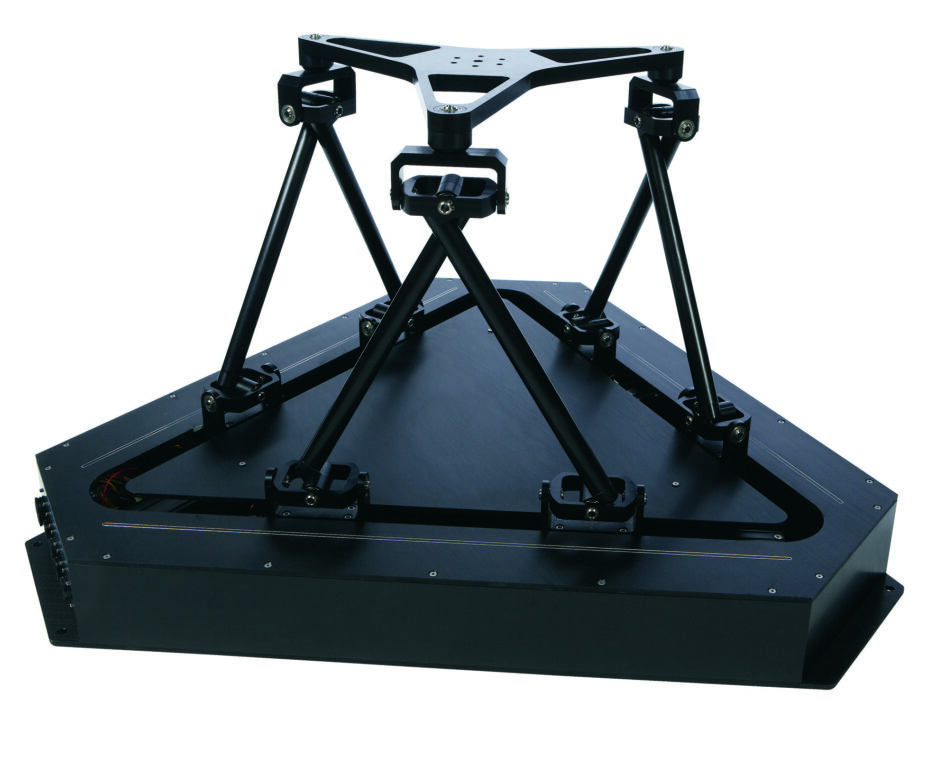
Product Details
The Hexapod is comprised of six linear ball-screw actuators driven by six DC motors. The ball-screw is based on a high-quality, low backlash linear guide with a total travel of 30 cm and is driven by a high torque direct drive motor. A revolute joint fastens the arms to each motor. For maximum safety, a motor brake control employs the Hexapod’s brakes when the joints reach their limit. Motor position feedback for all six motors is provided by optical encoders that measure the angular position of the motor shaft. An optional six axes ATI force/torque sensor can be installed on the end-effector to capture measurements of forces and torques along all degrees of freedom.
- High precision ball screw mechanism
- High-performance built-in amplifier
- High-resolution optical encoders to measure the joint angles
- Easy interface through universal USB connection
- Optional six DOF force/torque sensor
- Easy integration of third party structures, sensors and actuators
- Safety brake logic circuit and built-in mechanical brakes
Dimensions | 1.1 m x 1.1 m x 0.75 m |
Mass | 100 kg |
Mounting platform radius | 25 cm |
Arm length | 37.5 cm |
Maximum payload | 100 kg |
Workspace¹ | ± 7.4 cm (x), ± 11.0 cm (y), ± 5.4 cm (z) ± 17 deg (roll), ± 15 deg (pitch), ± 27 deg (yaw) |
Maximum Cartesian speed² | 0.67 m/s |
Maximum Cartesian acceleration² | 1 g |
Operational bandwidth² | 0 – 10 Hz |
Lead screw pitch | 1 cm/rev |
Actuator maximum force | 403 N |
Actuator travel | ± 15 cm |
Encoder resolution (in quadrature) | 10,000 cont/rev |
Joint resolution | 0.1 μm |
¹ Assuming other five DOFs held at home position.
² Please contact Quanser for full operational bandwidth specifications.
The following additional components are required to complete your workstation, and are sold separately:
For Simulink
- QUARC® add-on for MATLAB®/Simulink®