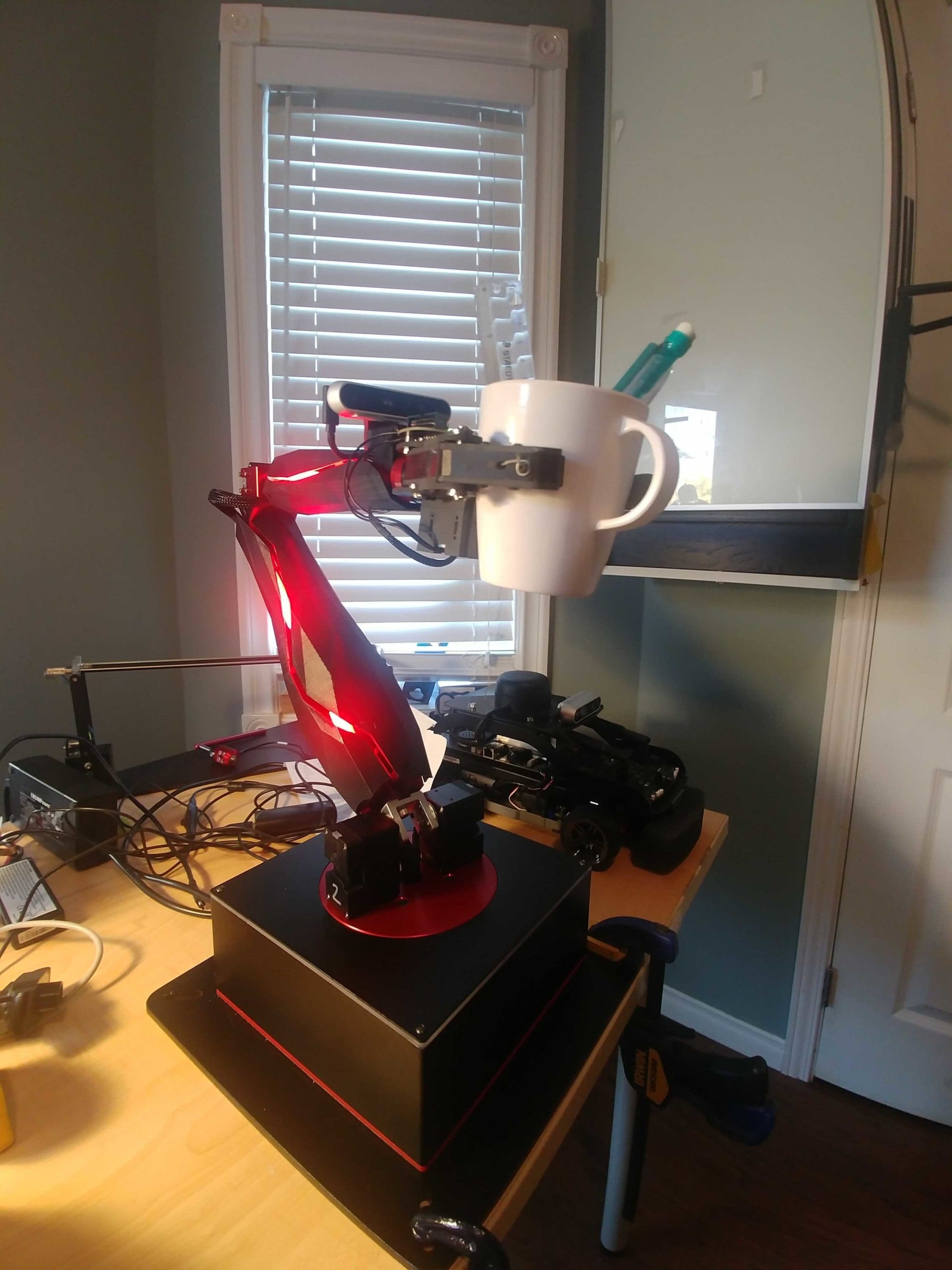
We have worked with quite a few arm manufacturers, such as Kinova, KUKA, or Denso in the past. Our open architecture via the rapid control prototyping software QUARC allowed you to use these devices from Simulink, designing your own algorithms or control techniques and validating them on hardware in real-time. We have also provided an efficient curriculum for these manipulators, based on classic teaching topics.
About a year ago, however, we felt a need to design our own manipulator, one that would be optimized for today’s teaching needs, as well as research trends. As the Academic Lead for the QArm robotic manipulator, I was presented with an opportunity to rethink the way we develop our curriculum for serial manipulators. In this blog post, I want to talk about the QArm, what we’ve done with the curriculum content, and how it could fit into your academic life. At the same time, I would like to thank all my colleagues involved in this process.
Teaching 1st and 2nd year
When I started my undergraduate engineering program back in 2008, the disconnect between our expectations and reality was apparent. We started our education, excited to tinker, and apply theory to industrial applications. The curriculum, though, was designed for traditional theory-based lectures and classes. A few labs made us analyze classic experiments such as an air-cart to measure gravity or the photoelectric effect. While I appreciated the simplicity of these experiments and what they stood for, they didn’t help us see how what we learned would apply to a modern world.
Instead, imagine being able to use a sophisticated yet user-friendly manipulator for high-level tasks that are focused on industry-relevant problems such as automated recycle sorting, and solve sub-problems like pick & place or task scheduling.
Pick and place task using the QArm manipulator and it’s virtual version
Right in the formative engineering years, student projects can include high-level multi-agent competition/collaboration based on connected systems, without diving deep into theory. Recently, McMaster University decided to do just that. Given the pandemic and safety considerations, they decided to continue using our virtual QArm (for virtual labs) for now. But the plan is to replicate this project using hardware once conditions improve.
Importantly though, McMaster students have access to modern curriculum structured around modern applications. My colleagues Simon Whitmell, Arman Molki, and Derek Wight were instrumental in developing cascaded content in Python with multiple user layers for varying levels of complexity and student background, all in time for the fall 2020 semester.
Sorting recycled waste using smart systems at McMaster University
Teaching 3rd and 4th years
Moving on to the third and fourth years, where courses dive deeper into the theory specific to manipulators, the QArm fits perfectly into existing courses with little to no modification. The QArm comes with a series of labs focused around curriculum topics such as forward/inverse kinematics, differential kinematics, statics, singularity identification, and dynamics.
Being the Academic Lead for developing this content, I wanted to ensure that the students keep sight of how these concepts relate to industrial applications. Therefore, every lab is taught via industry-relevant applications such as Lead Through, Teach Pendant, Tool Manipulation, Load Balancing, and Visual Servoing that relate to welding, assembly, spray painting, palletizing, payload transfer, etc.
Together with my colleague Thomas Zhang, we spent numerous hours debating the concept summary, lab procedure, and overall workflow in these labs to ensure that the ‘aha’ moment is not just a summary event but a constant experience. Take a look at the following video from a Singularity Identification lab that demonstrates how the end-effect loses a degree of freedom in the Y direction (blue line in the scope) when small speed commands are applied to the joints sequentially. Visualizing singularities as an adult made me want to provide this experience to students, and I am glad we did. Note that all the labs can be deployed to both the QArm and its digital twin, QLabs Virtual QArm.
Singularity Identification on the QArm
Singularity Identification on the virtual QArm
To compliment all this, my colleagues Andrew Jerabak and Filip Vranes wanted to ensure that students do not just use the QArm from afar. They wanted to give them personal experiences interacting with these manipulators in a manner that enhance their experience. The safety of students and the arm itself was vital while making the arm feel approachable. Thanks to them, the QArm uses a combination of powerful actuators and low inertia links. The actuators have multiple levels of safety via position/speed/acceleration limits and safe operating torques, allowing you to operate the arm in position mode for safe teaching applications. At the same time, the links are carbon-fiber skeletons covered with a facade that looks like a human arm, not that of a terminator.
Graduate Studies and Research
You can explore research topics focusing on digital-twin-based fault-tolerance, cobot/collaborative robotics, multi-agent communication/network safety, and smart systems. Research applications and their needs vary from group to group and project to project. My colleague Heidi Wight wanted to provide a variety of options for research teams and designed the breakout PCB with a single focus: improving expandability and connectivity. Thanks to her efforts, you can connect additional sensors/actuators to the end effector via numerous analog and digital I/O pins (USART, UART, SPI, and I2C) as well as 3.3V, 5V, and 12V power pins, all available in a compact form factor.
Filip Vranes also played a role in exposing open-architecture PWM and current operation modes for the QArm, so that researchers could develop and explore their own control strategies. Jason Desouza designed a tendon-based gripper with two articulated fingers for a 5-point-of-contact grip, allowing it to fold around objects of numerous shapes with ease. He wanted to ensure that the arm can function for extended periods of time. Instead of just providing a ‘safe’ low-end number for payload and operation time, he took the added time to test the arm under various operating conditions. Depending on operating trajectories, you can use the arm indefinitely with payloads up to 250 grams, for 20 to 30 minutes with payloads up to 500 grams, and for up to 10-15 minutes for payloads up to 750 grams. The bottleneck, of course, is the heat in the actuators, which requires rest periods, but, hey, 750 grams is no joke.
Within your reach and ready to grasp
Brought to you by a team of engineers passionate about improving engineering education while catering to custom research needs, you can tell just how much thought we have put into this. Last but not least, this was made possible by the sanity of my colleague Peter Martin, thanks to whose mediation and insight, the rest of us could fit our personal agendas side by side all into a single experience. The QArm is now ready for your use, and I can’t wait to hear what you think about it.