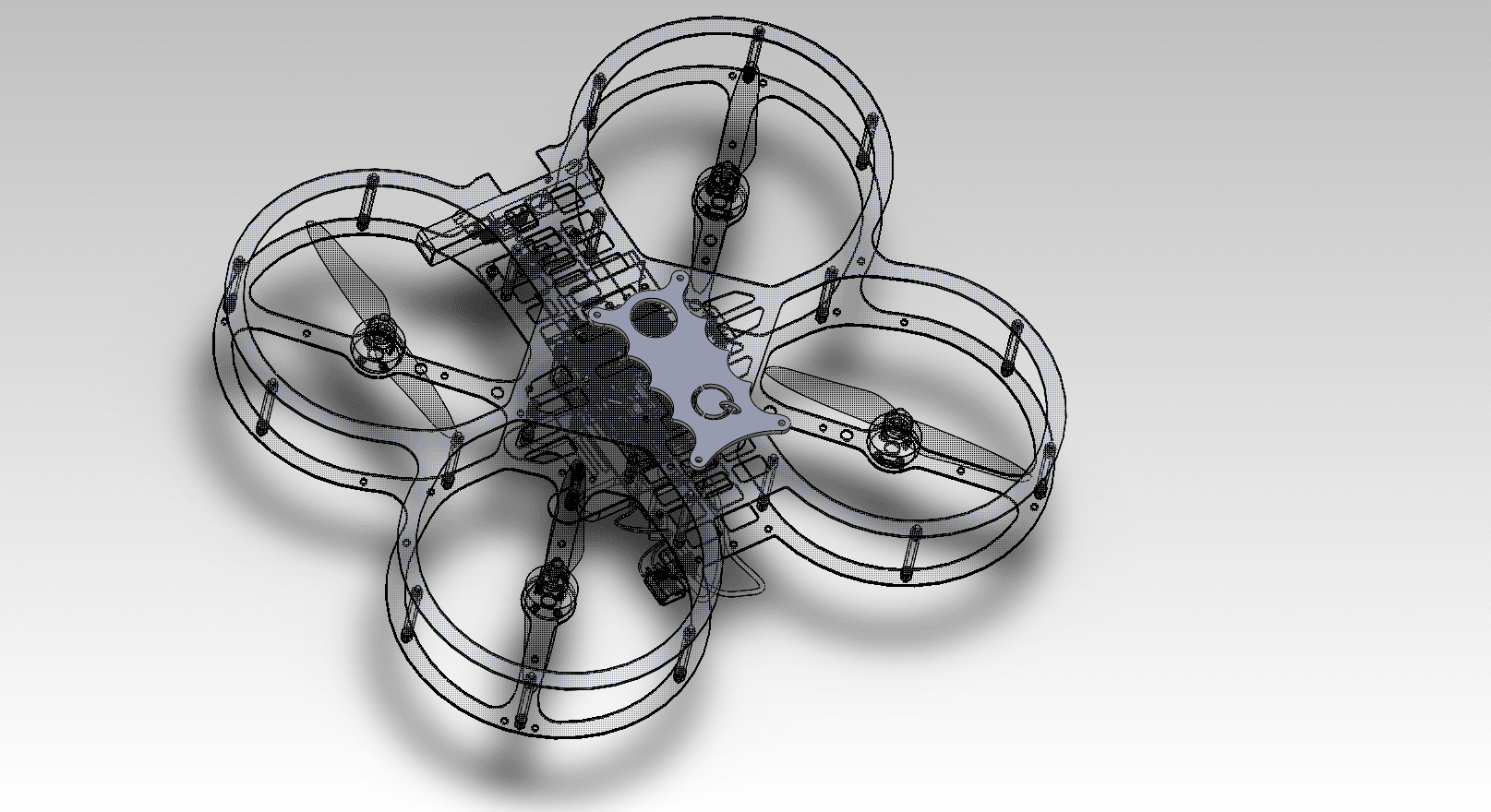
Over the past eight months, I’ve worked on the development of the Autonomous Vehicles Research Studio as part of the mechanical engineering team. We engineers design, test, and then constantly improve our work by iterating on the design at hand.
Design Approach
My first task as a design and test engineer was to come up with frame design for the new quadrotor, QDrone. I soon found out designing a drone was easier said than done. At first, I made concept sketches and SolidWorks models but realized it was better to start by building some prototypes so I could get a better understanding of how drones come together.
We wanted to design the QDrone as a powerful device capable of performing agile maneuvers in flight while being very durable. Normally, for a drone to be highly maneuverable, designers remove all non-essential weight to reduce both the stress on the mechanical components but also the power draw on the battery.
So my design iterations focused on dropping the excess weight, testing different materials for durability, and removing vibration going into the IMU.
Right Tools to Accelerate Testing
I also needed to figure out how I was going to validate if what I had built worked. That was where having a tool such as QUARC rapid control prototyping software really accelerated the design process. QUARC gave me quick access to I/O blocks such as analog read for battery status or PWM write to command the motors. Soon I was able to generate a simple but effective model to test my latest design iteration.
Our Approach to Testing
The first part of testing focused on the robustness of the quadrotor, so we took the QDrone and flew it as fast as possible against the wall….
Figure 1: QDrone wall impact to test the durability of frame and propellers.
Why did we do this? Because when a researcher is testing out an algorithm for machine learning, for example, the first couple of times the QDrone will fail. We wanted to make sure that the researcher could trust the system to be reliable and robust enough to crash multiple times and continue working.
We were also testing the durability of the frame and the propellers used. Using the knowledge from these destructive tests, we addressed as many of the mechanical failure points as we could.
Figure 2: QDrone deflection test.
The second priority of the design was to ensure the response of the drone was as dynamic as possible. That proved to be equally challenging but achievable. Stress testing the battery by cycling the motors from zero to full thrust was one test we performed. By using QUARC, we were able to design a battery stress test and in turn, study the response of the QDrone depending on how we cycled throttle from high to low. Utilizing QUARC allowed me to change the duration in which each cycle was high while maintaining a small duration of low. Likewise, if I wanted to increase the computational load on the system, QUARC made it simple to access more of the on-board sensors in the Intel Aero Compute Board.
Figure 3: Battery voltage cycle results using 0.2 second duration for motors on high.
After multiple design iteration and testing, we ended up with a fairly unique design of the QDrone not so stripped-down drone for highly dynamic motion but also not overly engineered for carrying heavy payloads. But still, it is just one part of what the whole research studio is about. To find out more about what the Autonomous Vehicle Research platform can offer, I welcome you to read our white paper – Thinking and Talking Multi-vehicle Research.